Welding Process
Perfect United for Unparalleled Strength
Creating the Best with Smooth Welds and Fine Surfaces
Our service offerings encompass a wide range of OEM production, including welding services. TGQ has extensive experience in CO2 welding, complemented by fully automated welding processes with robotic arms.
This allows us to take pride in delivering smooth welds and exquisite surfaces. We have served various industries, including automotive, medical device, and electronics.
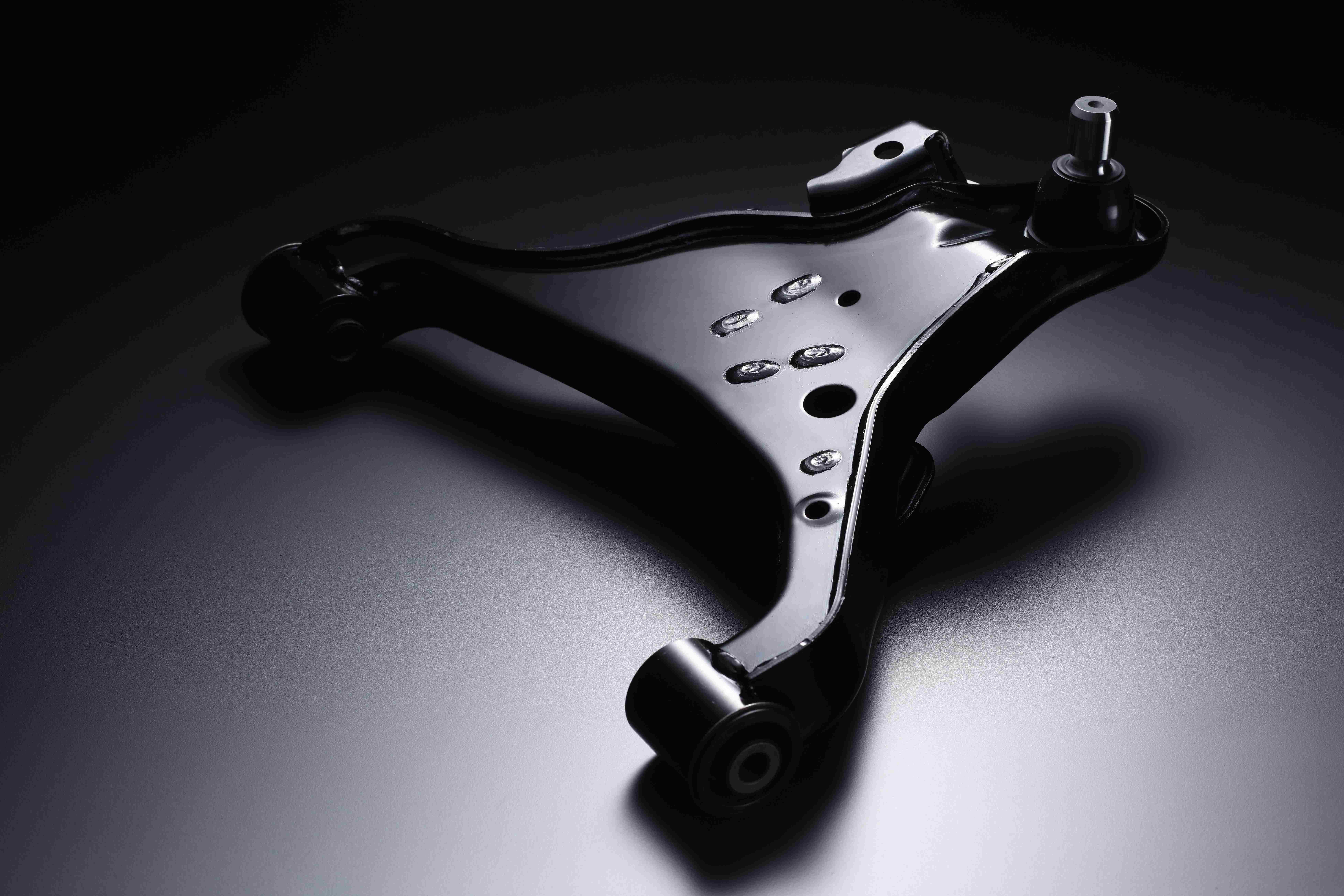
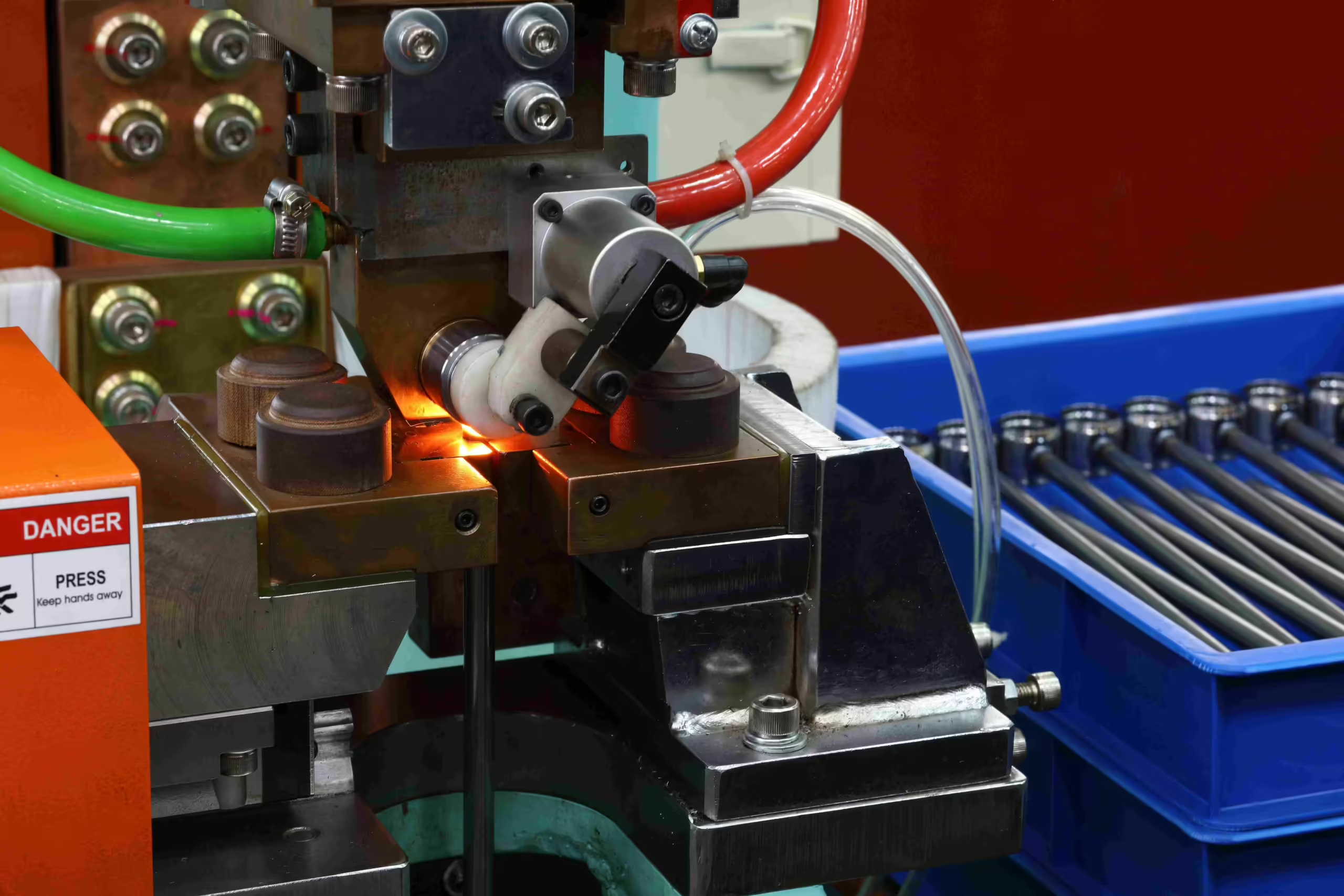
TGQ doesn’t settle for conforming to standards; we continuously challenge ourselves. As a company certified with ISO 9001 and ISO 14001, we uphold the philosophy of “Reliable Parts, Reliable People.”
Leveraging Japanese robotic arms, we ensure our products surpass high-quality standards.
Furthermore, we can choose the best welding methods based on the application to enhance production efficiency and quality stability, striving to satisfy our customers.
Our team can assist you in completing one-time projects or designing a customized welding approach using various materials to meet your needs.
Welding
To join two separate objects, there are many methods available, such as welding, screws, adhesives, and more, each with its advantages and disadvantages. Welding refers to the method of melting and joining into one piece through high-temperature heating, making it the most rigid bonding method in terms of structural integrity.
Types of Welding
For a quick overview of welding methods, we can refer to the simplified classification chart below:

The working principle of arc welding is akin to lightning, utilizing a potential difference to generate intense spark discharges, resulting in temperatures exceeding 3600°F and producing intense light. This method generates stable heat energy, melting the base material and the welding rod to create a bond.
Arc welding can be further divided into shielded metal arc welding and gas-shielded arc welding. The former has lower mechanical costs, but the intense light and gases produced during operation can impair visibility, making it challenging to accurately judge the welding point and affecting the stability of the welding rod, leading to reduced quality. Gas-shielded arc welding was developed to address this issue.
Gas-shielded arc welding can be categorized into TIG, MIG, and CO2/MAG. In terms of efficiency and ease of operation, TIG stands out. However, MIG excels in welding thin plates with a minimum thickness requirement of 3mm.
As for the difference between “MIG” and “MAG,” we can understand it through the terms. “MIG” stands for Metal Inert Gas, while “MAG” stands for Metal Active Gas. The distinction lies in the type of shielding gas used: the former employs inert gases, while the latter uses a CO2 mixture.
Advantages
Advantages of MAG
Cost-effective compared to MIG
Faster welding speed
Concentrated arc
Deeper penetration into base material
Fewer impurities and slag
Stable current and consistent quality
Effective rust prevention
The Disadvantages of Welding
・Generates strong light during operation
・Spattering of dust
TGQ addresses the drawbacks mentioned above of MAG using automated robotic welding arms. Our professional welding capabilities enable us to meet various requirements in different fields. Whether it’s components that need to withstand gravity, such as control arms and liners, under “safety” conditions, or items with “aesthetic” requirements like appliance housings and home decor, we can confidently handle them all.
Materials
Material Code |
JIS/SAE No. |
Material Category |
Material Name |
Hardness (HRB) |
Tensile Strength(N/mm2) |
Elongation |
SPHC |
JIS G 3131 |
Plate |
Hot rolled steel plate |
55~70 |
270 |
29% |
SAPH440 |
JIS G 3113 |
Plate |
Hot rolled high-tensile (black plate) |
75~90 |
440 |
32% |
S50C |
JIS G 4051 |
Plate |
Carbon steel for Machine Structural Use |
179~235 |
608 |
18% |
Equipment
Equipment | Specification | Quantity |
Japan OTC | Automated CO 2 Welding | 4 lines |
Production Capacity
- Minimum Batch: 100-1,000 pieces
- Maximum Capacity: 10,000-100,000 pieces per month

Here, clients can get various processing recommendations for different components and sizes. Our experienced team will invite you to collaborate on component design and modifications to conform to your requirements while managing your budget. To ensure customer rights and satisfaction, all processing services at TGQ are executed on a project basis. Therefore, you can confidently rely on us to help you achieve your goals.